Quality Risk Management (QRM) is a systematic process to assess, control, communicate, and review the risks to the quality of pharmaceutical products (medicines). It is applicable for both Timelines proactively and retrospectively. Quality Risk Management in Revised Schedule-M is a main addition by the central drug regulatory body (CDSCO) in India that is applicable from Jan 05, 2025.
The QRM shall ensure the protection of the patient by evaluating the risk to the quality of the product based on the scientific facts experienced towards the product quality deterioration.
Product Quality Review in Quality Risk Management in Revised Schedule-M
Regular quality reviews of all pharmaceutical products, including those meant for export, are necessary to ensure the consistency of production processes and the appropriateness of current specifications for both raw materials and finished products. These reviews aim to spot trends and identify possible improvements in products and processes.
Typically, these reviews should be done and documented every year, considering past reviews. The review process should include at least the following:
- Starting Materials and Packaging: Check the materials used, especially those from new sources, and ensure the traceability of active substances.
- Process Controls and Results: Review critical in-process controls and the results of finished products.
- Non-conforming Batches: Investigate any batches that did not meet the set specifications.
- Deviations and Non-conformances: Look into significant deviations or non-conformances and assess the effectiveness of corrective and preventive actions taken.
- Process and Method Changes: Review any changes made to processes or analytical methods. Evaluate the positive or negative impacts of changes.
- Dossier Variations: Review submitted, granted, or refused dossier variations. It will help to control future mistakes in the process.
- Stability Monitoring: Assess the results of the stability monitoring program and any negative trends.
- Quality Issues: Review quality-related returns, complaints, and recalls, along with their investigations. Document them for future reference to avoid any risk to the product quality.
- Previous Corrective Actions: Check if previous corrective actions on product processes or equipment were adequate.
- Post-marketing Commitments: Look into new dossier commitments and variations.
- Equipment and Utilities: Assess the qualification status of relevant equipment and utilities like HVAC, water, or compressed gases, and review their monitoring results.
- Technical Agreements: Ensure that all technical agreements are current.
The manufacturer must evaluate the review results and decide if any corrective and preventive actions or revalidation is needed under the product quality system. These actions should be completed promptly and effectively, following documented procedures. Procedures for ongoing management and review of these actions should be in place, and their effectiveness should be verified during self-inspections.
Quality reviews can be grouped by product type (e.g., solid dosage forms, liquid dosage forms, or sterile products) if there is scientific justification. A technical agreement should define the responsibilities of all parties involved in the quality review. The authorized person responsible for final batch certification must ensure that the quality review is accurate and completed on time.
Call us for upgrade your current pharma unit as per Revised Schedule M or for a setup of new pharma unit:
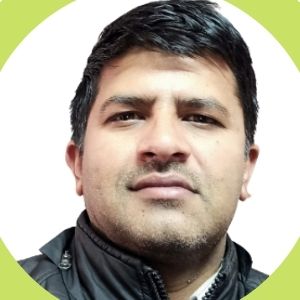
Darshan Singh is a professional pharmaceutical blogger from India having long experience of 20 years in the pharmaceutical field. He completed his Master of Science in Chemistry in 2003 from Kurukshetra University Kurukshetra.